Smoothest I.T.O. for Oled and Solar Applications
Thin Film Devices founder, Saleem Shaikh, was the first to use magnetron sputter Indium Tin Oxide (I.T.O.) for display applications, in 1976, while working for Sharp Co. (Japan). The smoothest surfaces were required as the structure and geometrics got smaller and smaller on active devices, with multiple structures, such as TFT, TFEL, Photo Voltaic, Oled, MEMS, and others.
Thin Film Devices uniquely incorporated the Ion Beam Sputter (IBS) process, in-line process for transparent conductors of I.T.O. (Indium Tin Oxide) I.Z.O. (Indium Zinc Oxide), A.Z.O. (Aluminum Zinc Oxide). For Dielectrics, such as Si02 (Silicon Dioxide), Silicon Oxynitride (Si0N), Silicon Nitride (Si3N4), Aluminum Oxide (Al203), Niobium Oxide (Nb203), Titanium Oxide (Ti02), Tantalum Oxide (Ta205), and for Metals, such as Al (Aluminum), Cr (Chromium), Mo (Molybdenum), Ni (Nickel), NiCr (Nichrome), NiCu (Constantan), Platinum (Pt), Pladium (Pd), Gold (Au), and many others.
The unique Ion Beam Sputtering technique, has produced the lowest surface roughness, on all of the films, which allowed fine features, ≤ 5 µm and smoothes possible surfaces.
IBS – Magnetron Sputtering in combination with an ion gun provides an improved sputtering process. Only this method can satisfy quality required by today’s advanced display/solar products.
The IBS energy levels of the magnetic sputtered atoms and ions are 5-10 times higher compared to conventional thermal evaporated films using electron beam and resistive sources. This unique technique of producing thin film produces many improvements in the films.
NO. | DESCRIPTION | TYPICAL THICKNESS | ROUGHNESS* AFM |
---|---|---|---|
1 | Standard ITO on 1737 glass | 1500Å 3000Å |
7±1Å 8±1Å |
2 | IMITO™ to LC | 1200Å | 5±2Å |
3 | BBAR | 2500Å | 20±5Å |
4 | Black Cr. (Cr203 + Cr) | 3000 + 2000Å | 30±5Å |
5 | Black Nb203 | 2000Å | 12±3Å |
6 | Low Temp ITO on glass | 1500Å | 5±2Å |
7 | Low Temp ITO on plastic | 1500Å | |
*Roughness was measured by 3 different independent sources |
- Improved Compact Density
- Low Surface Roughness (See Below)
- Splatter Free Films
- Films Keep Initial Alloy Ratio
- Corrosion Reduced with Small Grain Size
- Superior Adhesion and Durability
- Low Temperature Process Capability
- Unmatched Surface Roughness of Typical TFD Coatings
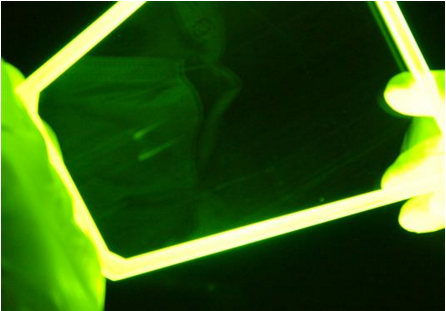
TFD ITO under 10K Lux without any haze.
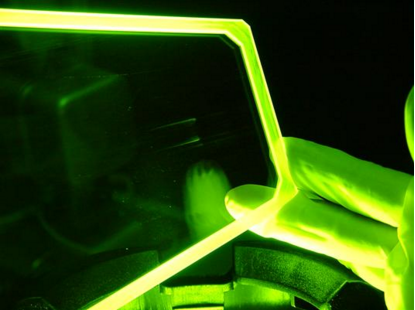
TFD ITO under 10K Lux without any haze.
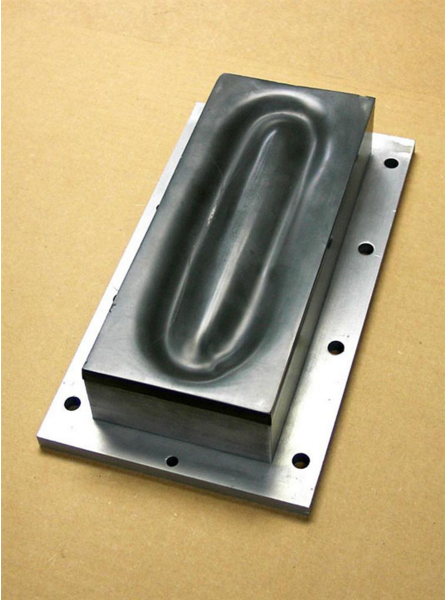
ITO Target without any nodule
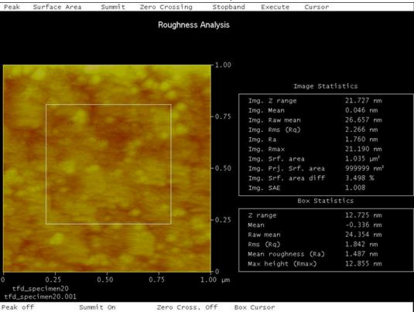
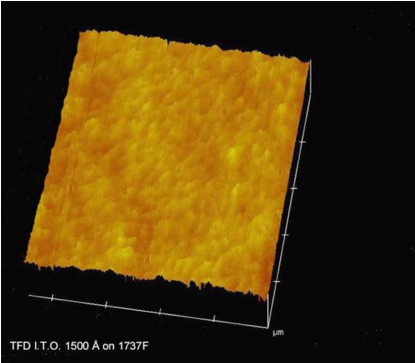
TFD ITO under 10K Lux without any haze.